
Thermal stability is required to minimize size variations due to temperature change which is caused by heat producing sources such as motors, electrical components or hydraulic circuit. This high dynamic rigidity (= damping) is also essential for high surface finish accuracy and extended tool life.
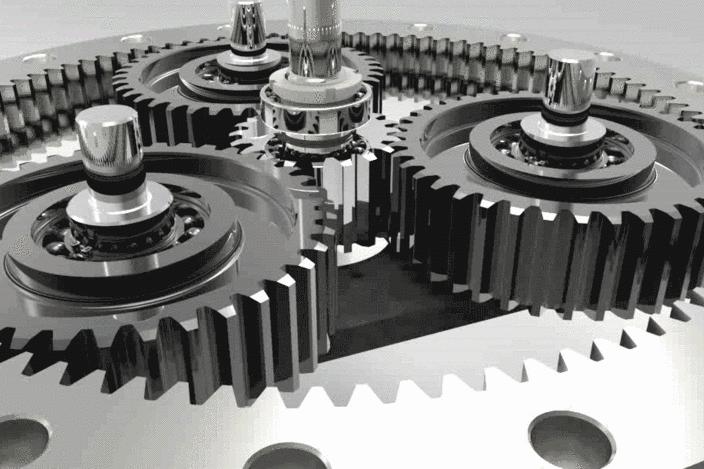
This stiffness is absolutely necessary to dampen as much as possible vibrations at the cutting tool. The Hembrug Mikroturn machines have a very high static and dynamic stiffness to absorb the high process forces that are released when machining hardened steel. What conditions do the Hembrug Mikroturn finish hard turning lathes meet?

Only a machine specifically developed for finish hard turning can absorb these forces. The “push back forces” or thrust forces are very high in finish hard turning. This leads to a drop-off in size tolerance capability, form inaccuracies, higher surface finishes and increased tool wear. Conventional precision turning machines are not designed to handle these higher forces (premature wear of the guideways). A higher cutting force results in a significantly higher push back pressure on the guideways. The relative cutting forces, the force required to pull the material away from the workpiece, are higher in hardened steel than in soft steel machining. – Workpieces with accuracies in the sub-micron range – Higher productivity due to inherent platform stability requiring fewer adjustments – Consistent piece to piece repetitive part accuracies – Longer tool life thru a highly damped platform When compared to other precision lathes, the unique hydrostatic slide and spindle design of the Hembrug exceeds all others. However, to develop the full potential of finish hard turning in terms of workpiece quality and process reliability, a lathe specifically designed for finish hard turning is necessary such as Hembrug Mikroturn lathes.

In principle, hard turning is possible on any precision turning machine.
